Transforming Sanitation Efficiency with Low-Pressure Cleaning Technology
in a Ready-to-Eat Facility
Significant reductions in cleaning time, energy consumption, water usage, & maintenance costs
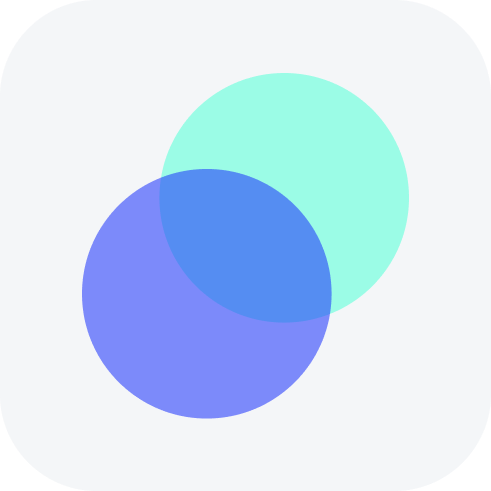
Client:
U.S.-based Ready-to-Eat (RTE) Food Production Facility
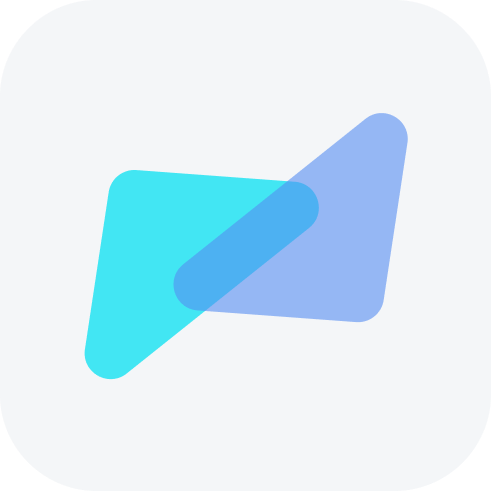
Industry:
Food Production – Ready-to-Eat (RTE)
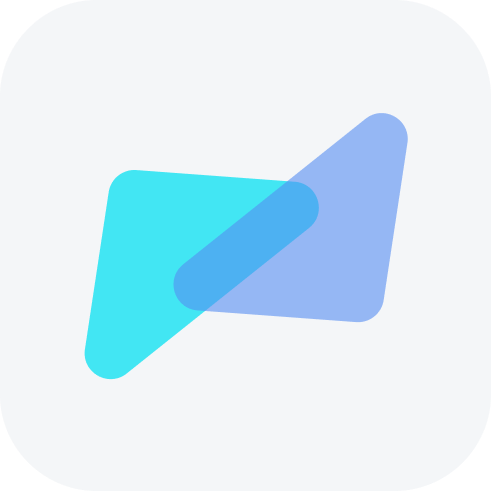
Scope of Work:
Cleaning Technology Implementation, Process Efficiency Improvement, Resource Optimization
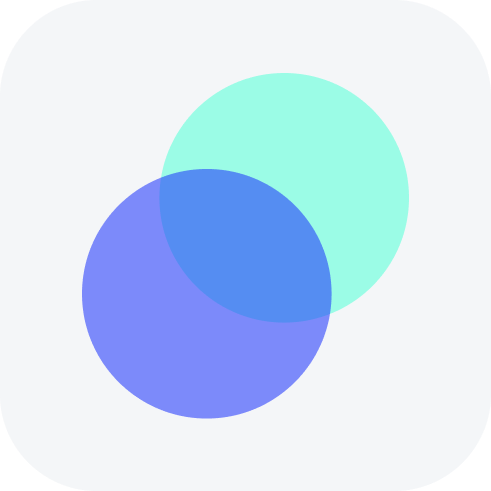
Outcome:
Significant reductions in cleaning time, energy consumption, water usage, and maintenance costs
Background
The RTE food production industry demands rigorous sanitation protocols to ensure product safety and compliance with food safety regulations. One U.S.-based RTE facility sought a more efficient, sustainable cleaning solution to enhance sanitation effectiveness while reducing resource consumption. GLJ INNOVATIONS introduced a low-pressure cleaning technology to address these needs, dramatically improving the facility's cleaning operations.
Challenges
The RTE facility faced several sanitation and operational challenges: High Resource Consumption: Traditional high-pressure cleaning systems consumed significant amounts of water and energy, leading to substantial utility costs. Extended Downtime for Cleaning: The high-pressure method was time-consuming, impacting production schedules and reducing operational efficiency. Maintenance Demands: High-pressure cleaning equipment required frequent maintenance due to wear and tear, leading to additional downtime and costs. Environmental and Sustainability Goals: The facility aimed to reduce its environmental footprint by optimizing water and energy usage, aligning with broader sustainability objectives.
Approach
GLJ INNOVATIONS implemented a low-pressure cleaning solution tailored to the facility’s sanitation needs. This approach integrated innovative technology with best practices in sanitation, emphasizing efficiency, sustainability, and cost reduction.
- Assessment of Sanitation Requirements
Evaluating Cleaning Challenges: We began by conducting a comprehensive assessment of the facility’s cleaning processes, identifying high-consumption areas and inefficiencies within existing cleaning protocols.
Technology Suitability Analysis: Given the facility’s needs, we selected a low-pressure cleaning technology that could maintain sanitation standards while using significantly less water and energy. - Implementing the Low-Pressure Cleaning Technology
Customized Installation and Training: We oversaw the installation of the low-pressure cleaning system, ensuring it was tailored to meet the RTE facility’s sanitation requirements. Training programs were conducted to educate sanitation teams on optimal usage techniques, ensuring consistent application and adherence to protocols.
Process Redesign for Efficiency: We redesigned sanitation workflows to integrate the new technology effectively, reducing cleaning time and streamlining workflows across the facility. - Optimizing Resource Usage and Reducing Costs
Water and Energy Savings: The low-pressure technology utilized a fraction of the water and energy required by traditional high-pressure systems. By adjusting cleaning protocols, we achieved significant reductions in utility costs and supported the facility’s sustainability goals.
Reducing Maintenance Needs: With less strain on equipment, the low-pressure system required minimal maintenance, decreasing downtime and cutting repair costs.
Results
The introduction of low-pressure cleaning technology delivered measurable benefits, significantly enhancing the RTE facility’s efficiency and sustainability: Reduced Cleaning Time: The new system decreased cleaning time by over 30%, allowing the facility to extend production hours and increase overall output. Lower Water and Energy Consumption: By shifting to low-pressure technology, the facility reduced water usage by up to 50% and energy consumption by nearly 40%, leading to substantial savings and supporting environmental commitments. Decreased Maintenance Costs: With a less demanding system, maintenance needs dropped significantly, cutting costs and reducing unexpected equipment downtime. Enhanced Worker Safety and Comfort: The lower-pressure system provided a safer work environment for the sanitation team, reducing the risks associated with high-pressure equipment and improving ergonomic comfort.
Conclusion
This case study demonstrates the transformative impact of introducing advanced cleaning technology in a high-compliance environment. By implementing a low-pressure cleaning solution, GLJ INNOVATIONS helped the RTE facility achieve its sanitation goals while dramatically reducing resource consumption and operational costs. This project highlights the value of innovative, sustainable solutions for food production facilities, setting a new standard in cleaning efficiency, resource optimization, and cost-effectiveness.